Start page
Project’s purpose
Project's description
Project’s objectives
Achievement plan
Results
Contact
Versiunea in limba romana
|
Technical Proposed solution
PROJECT’S NOVELTY AND ORIGINALITY DEGREE consists in the possibility of using solar energy
for different processes of metallic and non-metallic materials processing technologies: heating, melting, burning.
The contributions are based on the critical analysis of actual stage where it results the importance and feasibility of
such equipment for materials heat processing based on non-conventional energy: solar energy. The type of the aimed constributions
is energy and economic efficiency, national and European
priorities.
The most important researches refer to some metals and refractory materials behavior at high temperatures;
also refer to some materials purification and the use of some chemical syntheses. In the figure it is presented the parabolic
reflector of a solar furnace. Almost 60 plate mirrors are automatic following the sun and they concentrate the light into the reflector.
The reflector concentrates sun’s rays light (heat) in order to produce approximately 1 MW and a temperature of 3300 °C.
The furnace can use this temperature to produce steel in the crucible without a complementary energy source for realizing the heat process.
|
Steel or aluminum production needs a great deal of energy quantities.
This is normally delivered of electric energy, natural gases or conventional fuels.
Solar furnace uses energy delivered of sun’s power.
In the image it can be noticed how sun’s rays can be focused towards the crucible where the ore is.
This is heated at a very high temperature until it melts and it can be founded later on. Pollution is practically
inexistent because solar energy is a pure form of energy. One of the most important applications of the solar furnaces
is materials melting with higher melting point.
|
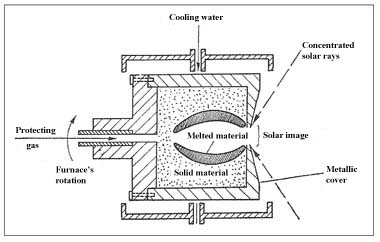
If the surface of a solid material is subjected to intense radiation from focus zone of a solar furnace it
take place the melting of the material on a section whose area is approximately equal to Sun’s image area.
Molten material quantity increases and forms a liquid cavity as heat gets into solid. Through such a process
it is possible the melting procurement into a crucible made exactly from the material which is to be molten;
this is cause to the existence of a high temperature gradient between the molten material and crucible’s exterior.
In conventional furnaces the crucible is heated from exterior, thus, it always has a higher temperature than the molten material.
That is why in such furnaces the crucible must be made from a more refractory material than the material which is to be molten.
In addition it must be chemically inert towards molten material. The achievement difficulties of these two conditions increase as
the melting point of the studied material is higher and over 2000 °C are few chances to avoid chemical reactions.
The use of the solar furnaces in melting materials with high refractoriness overbears these important limitations of the conventional furnaces.
Thus, melting can be realized in furnaces with horizontal axis. The furnace is rotated around the horizontal axis and has the interior
diameter several times bigger than sun’s image diameter. If the speed of rotation is low the molten material remains downside the furnace
and rotation helps to achieve a uniform distribution of heat. For higher speeds of rotation the molten material is centrifugally – forming
a cavity- which will not permit its discharge from the furnace. The exterior walls of the furnace -made of steel- can be cooled with
water for maintaining a high temperature gradient in the walls (if necessary). Under the situations when melting should realize a
certain protective atmosphere it is passed an adequate gas flow as indicated in the figure. Among the materials to be studied are: quartz,
zirconium dioxide, corundum, ceramic oxides and materials like carbides, nitrides and boron for which conventional melting techniques
present a series of inconvenient. As well it can be studied the practice possibility for using solar furnaces in steels melting.
Technically the crucible can be easily made by introducing into furnace cavity a refractory powder (like mullit) and sintering or even
melting it by centrifuging the furnace exposed to solar radiation. That is why scrap is introduced in furnace, it melts and then if
necessary it is molten. The performances of such a solar furnace must not be special because there is sufficient temperature
of 2000 – 2500 °C.
For future, a higher interest presents melting some other metals more expensive than steel like titanium, zirconium and molybdenum.
In this case it must be assured an inert protective atmosphere and thereby it must be taken into account
the complications and expenses related to these. Other applications of solar furnaces: impurities evaporation,
zonal melting, fractionates crystallization, zirconium oxide extraction from zircon (zirconium silicate) and the
materials study under thermal shock conditions.
|
Technical impact | Social and environmental impact | Economic impact |
Impact on technological development. Regionally
- Promoting regionally a high performance level and technologies/products quality by the collaboration between profile partners
situated in the same underprivileged zone;
- Increase of competitive level through re-engineering based on modernization and proper researches by initiating regionally the partnership
between economic agents and research-development departments.
Impact on scientific and technical background
- Increase of economic agents capacity to efficiently assimilate the last technologies and results of the research activity
- C-D department development of promoting activities for new materials and technologies and advanced processing,
analysis and control techniques.
|
- Social stability through economic background improvement;
- Creation of new work places for the graduated youth and perfection of work force to assure the technological transfer and
implementation of the proposed solution;
- Increase of bio-security and bioethics levels within the project of the economic agents’ responsible factors to strengthen labor discipline and environment protection
through personnel’s consciousness after UE adherence.
|
- Increase of economic efficiency for potential beneficiaries by diminishing materials processing and maintaining expenses for heat systems;
- Possibility of getting new contracts that assure investments and financial stability;;
- Expansion of applicability domain through diversification of solar systems used in industry
- Market position improvement of potential beneficiaries by promoting quality and competitiveness.
|
|
“Gh. Asachi” Technical University of Iasi
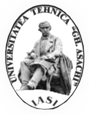
Project manager
Professor dr. eng Petrica Vizureanu
|