Start page
Project's purpose
Project’s objectives
Achievement plan
Proposed technical-scientific solution
Results
Contact
Versiunea in limba romana
|
Project’s description
The achievement of this project will make possible knowledge and new equipment integration from non-conventional
energies domain into industrial domain, with direct applicability in materials thermal processing.
Thus it can be said that this theme will “dissolve” the technical-scientific frontier
between non-conventional energies domain and materials heat processing one.
|
The scientific importance of the proposed theme is given by the non-conventional energies impact on the materials processing industry.
Solar energy is a very popular subject because mankind has realized that energy makes our existence
vital component under the conditions of modern civilization. The sun gives a possible alternative to energy crisis solving which
become more and more pronounced once with population growing, life standard, and technological development simultaneous with the
conventional fuel store exhausting (natural gases, petroleum, coal etc.)
|
The fundamental research character is based on the development of a new and original concept for Romania:
Thermal solar systems or solar furnaces which could be used at different
terrestrial applications: water heating, electric energy production through photoelectrical conversion, water distillation,
the bioconversion obtain of some fuels and chemical products, electric energy production with thermodynamic cycle, materials processing etc.
|
The name of solar furnace is given by a system made of an installation for solar radiation capture
and a receiver mounted in the focal zone where there are the highest temperatures. Lavoisier built the first solar furnace with
lens in 1772 reaching the platinum melting point (1773 °C).
Solar furnaces with reflecting concentrator type are the most practical and easier to make. The optimum reflecting concentrator
for solar furnaces has a revolution parabolic form.
|
The easiest geometrical arrangement is obtained when the parabolic mirror is mounted so thatthe axis is always pointed towards the Sun
with the help of a tracking system after two coordinates.
The most profitable constructive variant
economically speaking gets by mounting the solar furnace with the parabolic mirror’s axis horizontally to the North
(in Northern hemisphere, Romania).
|
The first modern solar furnace which used a parabolic mirror wide opened was built by Straubel in
1921 and used by Conn in 1935 for melting zirconium oxide. A solar furnace of impressive dimensions was built
at Odeillo-Font Romeu, France, situated in Pyrenees at 1820 m height where the annual number of clear days gets to
180 and the density of the incident radiant power reaches 1kW/m2.
It was in use since 1970 and gave a maximum power of 1000 kW in focus permitting the procurement of temperatures over 3500°C.
The furnace has a parabolic concentrator with fixed horizontal axis, its
focal distance being 18 meters, height of 40 meters and maximum width of 54
meters. It was used for a series of researches concerning metals and
refractory materials behavior at high temperatures; it was also used for
purifying some materials and to realize some chemical syntheses. In 1976 the
solar furnace was transformed into a solar-electrical station that gave to
France's energetic system an electric power of 64 kW.
|
There were also made other solar furnaces of small dimensions in France, USA, Japan and Egypt. These were used for the
study of refractory materials, special melting techniques for metals and alloys, reactions in gases, researches on the gas
syntheses etc. A chemical solar reactor was accomplished in 2004 at Paul Scherrer Institute (PSI) in a project named Solar
Production of Lime designed for reaction occurrence: CaCO3→CaO + CO2.
Rotary furnace consists in a steel cylinder with ceramic thermal insulation and which contains within work chamber a
highest temperature multi-tube system made of carborundum. Concentrated solar radiation gets through the circular opening of the
furnace and heats the cavity respectively the multi-tube system transmitting heat to the calcium ore particles.
Particles with dimensions between 1-5 mm were processed producing high purity lime with a burning degree of 98%.
Work temperature: 1200–1400 K.
|
The agents that influence solar furnaces performances used in industrial application that impose the
procurement of some high densities of radiant power and thus need a geometrical perfection for the concentrator are
divided in three categories:
|
- The first category is based on basic geometry of the parabolic concentrator, defined of focal distance f and its opening D. Once they were chosen it results the solar image dimensions,
focusing factor, and maximum ideal values for temperature and radiant power density
within image regardless concentrator’s construction and installation place.
|
- The second category contains the factors that reduce the performances of the solar furnace cause to its construction and its installation place.
These factors are: atmosphere’s transmission energetic factor, energetic factor of mirrors’ directional reflection and geometrical
perfection index of the parabolic concentrator.
|
- The third category includes the factors related to receiver’s properties: energetic factors of absorption and emission
and conductive and convective heat losses.
|
The potential available power Pf in Sun’s image from the focal plan of a solar furnace is given by the relation:
Pf = πRdDaE0f2θmax
where:
Rd – Energetic factor of parabolic mirror’s directional reflection (including heliostats if they exist);
Da – Atmosphere’s transmission energetic factor in furnace’s installation place;
E0 = 1353 W/m2 – solar constant;
f – focal distance;
θmax – opening angle for parabolic concentrator.
If it is disposed a solid corps in solar image the fraction from potential available energy effectively
absorbed by the corps would be determined by the absorption factor and the corps-receiver form itself.
As such maximum temperature which could be reached into a solar furnace depends on the receiver’s properties
situated in furnace’s focal area:
Tmax = TS(RdDa)¼(sinθmax)½
where TS = 5800 K – Sun’s surface temperature.
The main application domains for solar furnaces are those that imply the procurement of some higher
temperatures and thermal flows. Solar furnaces offer,
in addition towards conventional furnaces, extremely advantageous work conditions like atmosphere which can be controlled,
studied material is slightly accessible, and polluted environment such as flames, electric and magnetic fields is absent .
|
|
“Gh. Asachi” Technical University of Iasi
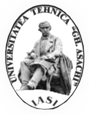
Project manager
Professor dr. eng Petrica Vizureanu
|